AD-IPC-7130
Chassis for ATX/MicroATX Motherboard.
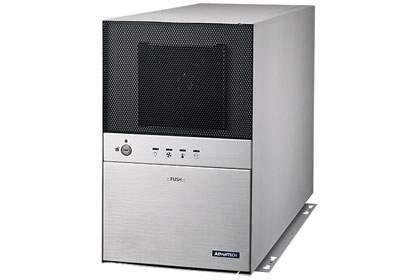
- Shockproof drive bays - One 5.25", 2 hot-swap 3.5" and 1 internal 3.5"
- Lockable front door to prevent unauthorized access
- LED indicators for system fault detection
- Bidirectional to mount chassis on the wall or workbench
- Built-in Intelligent System Module enabling whole system fan control and remote manageability
Datasheet
Product Specification
Model | IPC-7130-00B | IPC-7130-50B |
Physical Characteristics | ||
Weight | 12.8 kg | 12.8 kg |
Dimensions (W x H x D) | 200 x 320 x 480 mm | 200 x 320 x 480 mm |
Front I/O Interface | ||
USB 2.0 | 10 D-sub openings supporting up to 10 COMs with optinal COM cables | 10 D-sub openings supporting up to 10 COMs with optinal COM cables |
Cooling | ||
Air Filter | Yes | Yes |
Fan | 1 (12 cm / 82 CFM) + 1 (6 cm / 27.72 CFM) | 1 (12 cm / 82 CFM) + 1 (6 cm / 27.72 CFM) |
Environment | ||
Operating-Temperature | 0 ~ 45 | 0 ~ 45 |
Non-Operational Temperature | -20 ~ 60° C | -20 ~ 60° C |
Disk Drive Bay | ||
5.25 External Bay | 1 | 1 |
Hot-swap | 2 | 2 |
Miscellaneous | ||
LED Indicators | Power, HDD, temperature, fan | Power, HDD, temperature, fan |
Front Panel | Power, HDD, Temp, Fan | Power, HDD, Temp, Fan |
Power Supply | ||
Power Supply | - | 500W (Single) |